|
Head
Ing. Tomáš Chráska, Ph.D.
Tel.: (+420) 266 053 517
Email: tchraska@ipp.cas.cz
Deputy head
Ing. Jiří Matejíček, Ph.D.
Tel.: (+420) 266 053 307
Email: jmatejic@ipp.cas.cz
Main office
Institute of Plasma Physics of the CAS
Department of Materials Engineering
Za Slovankou 1782/3
182 00 Prague 8
Detached site
Institute of Plasma Physics of the CAS
Beranových 130
199 00 Prague 8
Tel.: (+420) 225 115 244
|
Research focus
|
The research at our department is focused primarily on a special field of materials engineering – interaction of plasma with solid and liquid phase. We are one of the few laboratories in the world engaged in plasma-material interaction at both major levels: interaction of materials with high-temperature plasma (for example in fusion devices, such as tokamaks), as well as plasma technologies for preparation of new materials, using so called low-temperature (thermal) plasma.
|
|
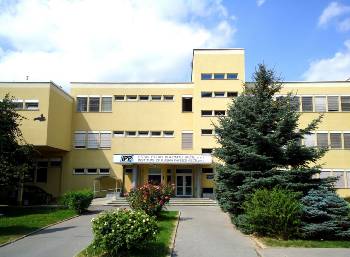
Location: Za Slovankou 1782/3 Map
|
Staff |
|
|
Fusion applications – plasma as a “problem”
During their interaction with plasma, materials undergo various surface and volumetric changes, which may complicate the operation of construction parts under long-term exposure to plasma.
These issues are highly relevant in current or planned high-power fusion devices –tokamaks. To increase the lifetime of plasma facing components, for instance, we develop so-called functionally graded materials (FGMs), which are generally layered structures combining for example refractory properties of tungsten with the mechanical strength of steel or the thermal conductivity of copper. For testing the behavior of these materials in tokamak plasma, we use a special port of tokamak COMPASS at our institute. Simulated loading, e.g. by laser or electron beams, is performed in collaboration with domestic (Research Centre Rez, UJV Rez, Brno University of Technology,…) and foreign (Forschungszentrum Juelich - Germany, Dutch Institute for Fundamental Energy Research - Netherlands, ...) partners.
Plasma spraying – Plasma as a “tool“
On the other hand, high plasma enthalpy can be also utilized to deposit various materials by the plasma spraying technique. Materials in the form of powder, suspension, or solution are injected into a thermal plasma jet generated by a plasma torch. Once the material particles enter the plasma jet, they are subjected to various interactions with the plasma that raises their temperature, velocity and may also lead to chemical changes. A so-called “plasma sprayed coating” with typical thickness of 0.1 to 1 mm is formed after many of the particles deposit onto the component surface. Such coatings then improve the functional surface properties of the coated component, e.g. abrasion resistance, corrosion resistance, thermal and electrical conductivity etc. Patented fabrication of thin-walled free-standing ceramic shells or parts is a specialty of our laboratory.
Plasma spraying in our lab is carried out by the world's unique
water stabilized plasma (WSP) torch or newly developed
hybrid water (WSP®H) torch. Both of these torches were developed at our institute in cooperation with
ProjectSoft HK company that is in charge of their commercial sales to end users.
Spark Plasma Sintering of powder materials
Our lab was the first one in the Czech Republic that started using Spark Plasma Sintering (SPS) technique to fabricate bulk materials from powders. This technique is also called Field Assisted Sintering Technique (FAST). It uses pulsed electric current and increased pressure to sinter metallic and non-metallic powders in graphite dies. The sintering can be done at temperatures of up to 2400°C using very high heating rates and thus in considerably short times. SPS technique is remarkably suited for fabrication of pure ultrafine-grained materials and special composites.
Academic cooperation
Experimental work at the ME department is carried out in a wide domestic and international cooperation. We benefit from a long term cooperation in the field of plasma spraying and fusion materials with prestigious laboratories and universities in the USA, Germany, France, Sweden, Finland, etc. The cooperation takes the form of sample fabrication and exchange, materials characterization and analyses, and also students exchanges and research internships.
Our cooperation with other institutes of the Czech Academy of Sciences and Czech universities is also quite important. For example we participate in the Center of Excellence “Multidisciplinary research centre for advanced materials” and the Center of Competence “Research center of surface treatment”.
Industrial cooperation
We design and fabricate special plasma coatings for specific applications for a number of Czech companies. We also carry out contractual material analyses and consultations.
Did you know that ...
-
Since 2012, we operate our detached Laboratory of Plasma Technologies (LPT) in Prague – Letňany.
-
The plasma emerging from our water stabilized plasma torch has a temperature of over 25,000 ° C. This makes it possible to effectively spray materials with high melting point such as tungsten and oxide ceramics.
-
Power consumption of the WSP torch and other supporting devices is over 200 kW, which enables to deposit a large amount of powder material (tens of kilograms per hour) onto large surfaces.
-
The water stabilized plasma torch is a very strong source of UV light and generates noise levels above 120 dB. Therefore the WSP torch is operated in a soundproof concrete spray booth.
-
Our department is well equipped for a thorough characterization of all starting and processed materials. We can do measurements of grain size distribution, phase analysis, microstructure characterization, determination of mechanical, thermal, and selected physical properties.
-
We develop new methods of characterization for our materials.
-
We can fabricate not only research samples but also custom parts for real industrial operation.
-
Thanks to our intensive collaboration with partner institutions in Czech Republic and abroad, we have hands-on experience not only with plasma spraying but virtually with all other conventional thermal spray techniques.
-
The SPS machine can heat samples with maximum current of 4000 A and reach heating rate of several hundreds degrees per minute. The maximum powder sintering temperature is 2400 °C.
-
We have prepared more than 1200 different samples during the first three years of SPS operation.
-
We have patented a number of technological processes, as for example fabrication of nanocrystalline ceramics, thin-walled free-standing ceramic shells, ...
- Our goal is not “only” to do high quality basic research but also to transfer our knowledge and findings to solve the real world technical problems.