Department of material disintegration
Ing. Josef Foldyna, CSc. | ||
Ing. Vladimir Foldyna Bc. Lucie Gurkova Ing. Petr Hlavacek, Ph.D. Prof. Ing. Sergej Hloch, Ph.D. | Ing. Jiri Klich, Ph.D. Ing. Dagmar Klichova Ing. Dominika Lehocka, Ph.D. Daria Novakova | Ludek Pivoda Ing. Zdenek Riha, Ph.D. Ing. Libor Sitek, Ph.D. Ing. Michal Zelenak, Ph.D. |
The Laboratory of Rock Cutting was established in 1985 as a part of the Department of Mining Geomechanics. The original objective of the research was to study processes associated with rock and rock-like materials by mechanical tools and high-speed water jets. In 1992, the laboratory changed its name slightly to the Laboratory of Rock Disintegration and became part of a newly created Earth Material Sciences Department. With respect to specific research problems solved by the laboratory staff, the Department of Material Disintegration was established. The department is oriented entirely to the study of new, advanced technologies for material disintegration.
The department gradually established cooperation with domestic and foreign scientific workplaces (e.g. Brno University of Technology, VSB-Technical University of Ostrava, the University of Cagliari, the University of Applied Sciences of Northwestern Switzerland, Koszalin University of Technology, AGH Cracow) and industrial partners (e.g. PTV, NET, Hammelmann, Ecoson).
The RDIOP project Institute of clean technologies for mining and utilization of raw materials for energy use, in which the department has participated considerably since 2011, has represented another significant stimulus for further development of the department.
Main research topics
Research activities of the department are aimed in particular at the high-speed water jet disintegration of materials and geomaterials.
Intensification of high-speed water jet effects. Research activities are directed at the study of the dynamic behaviour of pulsating water flow, the definition of the natural relationship of the processes of excitation and propagation of high-frequency pressure pulsations in liquid, and their utilization for a generation of pulsating high-speed liquid jets.
Complex dynamic processes occurring during the excitation and propagation of high-frequency pressure pulsations in liquid are studied both theoretically, with the aid of numerical simulations and CFD (Computational Fluid Dynamics) methods, and experimentally, using the direct measurement of the frequency and amplitude of dynamic pressure in a high-pressure system as well as stagnation force generated by the impact of the pulsating jet.
The process of forming the pulse in a high-speed water jet downstream from the nozzle exit is studied with the aid of PIV (particle image velocimetry) and shadowgraph methods. The interaction of the pulsating jet with the material is studied using optical methods and image analysis to define both the processes occurring during the interaction and the properties of surfaces created by the effects of the pulsating jet. The cutting and disintegration effects of the pulsating water jets are tested on various materials to compare their performance with continuous jets and, eventually, with other technologies.
The objective of the research is to understand the fundamental processes of the generation and transmission of pressure pulsations in a high-pressure system, the formation of a pulsating jet and its interaction with material.
Abrasive materials for abrasive water jets. This topic covers research in the area of new abrasive materials (both natural and artificially produced). The properties and behaviour of abrasive particles in the processes of generating of abrasive water jets and material cutting are studied. The solutions to problems associated with the preparation, testing and recycling of abrasives is also represented in this field of activity.
The research is aimed at the definition of the crucial properties of abrasive materials from the point of view of both maximizing the cutting performance and minimizing the wear of the cutting head, the economic cost, and the negative impacts on the working and living environment. The objective of the research is the development of a new generation of abrasive materials.
Numerical simulation of flow. Compressible liquid flow in the nozzle for high-speed water jet generation represents the main application of numerical simulation in the department. Models, created using ANSYS software, allow for the study of liquid behaviour within the nozzle and downstream from the nozzle exit. Subsequently, the whole final assembly is optimized to obtain the best efficiency of the simulated system. Created modifications are verified by laboratory experiments.
Knowledge and skills obtained while using ANSYS software are also utilized for solving problems in cooperation with industry. The department offers help in a wide area of liquid flow and stress analysis. Our researchers are able to participate in the solution of various problems from the flow of compressible fluids through mixture and multiphase flows to combustion and heat exchange, etc.
Study of topography and quality of surfaces. This research is aimed at the study of the effects of technological parameters on the surface topography (roughness, waviness, etc.). The possibilities of influencing the properties of material surface layers by traditional machining methods, the application of liquid jet, etc. (the treatment of concrete surfaces for following repair work, the preparation of a suitable anchor profile, the hardening of the surface layers, the removal of residual stresses, usable and aesthetic qualities of surfaces, etc.) are also studied.
The effects of the parameters of cutting technology on the surface topography are studied in order to eliminate any negative effects of the technology on the properties of a work-piece. The relationships between force effects of the cutting technology on material, vibration, fluctuation in the operating pressure (in the case of water jets), acoustic emissions, etc. and the topography of the machined surface are searched for.
New areas of high-speed water jet utilization. This research is oriented primarily towards the use of the abrasive water jet to enable the machining (turning, milling, polishing, drilling, etc.) of difficult-to-machine and non-machinable materials, such as composites, ceramics, high-strength alloys, glass, rocks, etc.
Precise machining by an abrasive water jet to obtain the optimal geometrical and dimensional accuracy of a work-piece without the need for further machining represents another research activity in this area. Increased accuracy of final work-pieces can be achieved by using a more precise cutting head manipulator, a 3-D swing cutting head eliminating chamfer, an appropriate selection of nozzles, abrasives, etc.
The possibilities of preparing mineral and ceramic precursors for the synthesis of nanoparticles and carriers of nanoparticles with specific properties using disintegration by high-speed water jets, and the utilization of high-speed water jets for ultra-fine grinding and disintegration of materials in the area of production of micron and submicron particles, are also studied.
Selected scientific and application results
The generation of a pulsating water jet for the disintegration of material. The generation of sufficiently high pressure pulsations in pressure water upstream from the nozzle exit enables the creation of a pulsating liquid jet that emerges from the nozzle as a continuous stream, and it forms into pulses at a certain stand-off distance from the nozzle exit. The advantage of such a pulsating jet over the continuous one is based on the fact that the initial impact of pulses on the target surface generates cyclically an impact pressure that is several times higher than the stagnation pressure generated by the action of a continuous stream under the same working conditions. In addition, the action of a pulsating jet also induces both fatigue and shear stresses in the target material due to the cyclic loading of the target surface and the radial high speed flow across the surface. This further improves the efficiency of the pulsating liquid jet in comparison with the continuous one.
Therefore, the research was aimed at the above mentioned area and, as a result, an original method of a pulsating liquid jet generation was developed and tested extensively. The method is based on the generation of acoustic waves by the action of the acoustic actuator on the pressure liquid and their transmission via a pressure system to the nozzle. Research of the fundamentals of the process of excitation and the propagation of acoustic waves (and/or high-frequency pressure pulsations) in liquid via a high-pressure system and their influence on the formation and properties of a pulsating liquid jet was crowned by the granting of a Czech patent and the completion of a license agreement for the manufacturing of one piece of an acoustic generator of pressure pulsations.
The result was included in selected results of the basic and targeted research in the Annual Report of the ASCR in 2008.
Acoustic generator of pressure pulsations. The development and manufacturing of an acoustic generator of pressure pulsations for an operating pressure up to 150 MPa with excitation frequency of 20 and 40 kHz is continuation of the above mentioned results. The internal profile of the generator was optimised with respect to the maximum amplification of pressure pulsations in the liquid upstream from the nozzle exit using the CFD and FEM methods. In addition, a new shape of the ultrasonic sonotrode flange was designed to reduce the undesirable transmission of ultrasonic vibrations into the generator body.
The results obtained led to the signing of an exclusive license agreement on their usage with a renowned German manufacturer of high-pressure equipment. The result was also included in the selected results of basic and targeted research in the Annual Report of the ASCR in 2010.

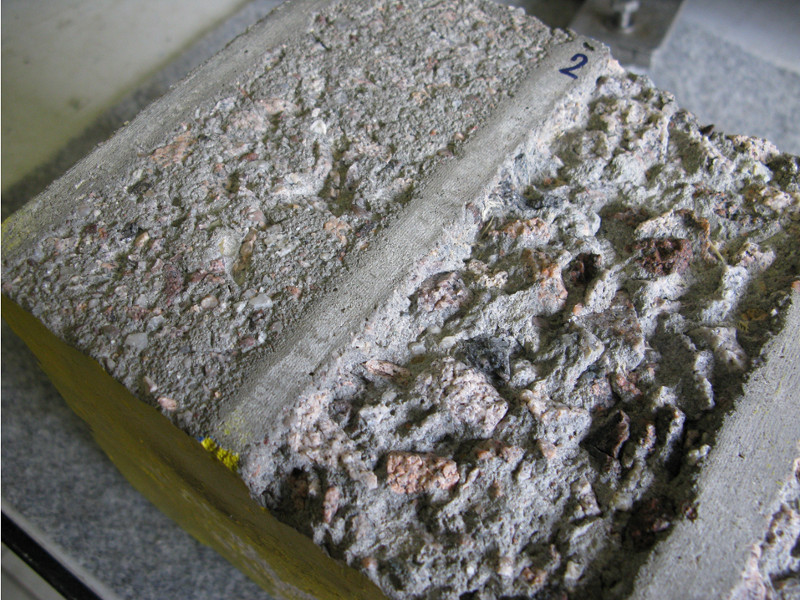
Removal of degraded surface layers of concrete by water jets. Laboratory experiments, concerned with the removal of degraded surface layers of concrete by high-speed continuous and pulsating water jets, were prepared in cooperation with the Brno University of Technology and VSB-TU Ostrava. Concrete blocks of precisely-defined properties were created; some of them were stored or tested by cyclic loading in different corrosive environments (freezing effect, the effect of chemical defreezing agents, the long-term effects of chlorides, sulphates and nitrates). Several testing samples were left as reference samples, i.e. not exposed to any corrosive environment.
The pulsating jet achieved a higher efficiency in all cases compared to a continuous jet under the same working conditions. However, the ratio of volume removed from the concrete test sample by both pulsating and continuous jets varied considerably according to the type and degree of sample degradation and the cutting parameters. While continuous jets removed only the upper part of the cement paste, pulsating jets penetrated deeper and removed cement paste to aggregates at given testing conditions. Thus, pulsating jets are able to remove selectively degraded concrete layers and preserve healthy concrete, following the application of repair coatings and mortars also at low water pressures. A higher roughness of the concrete substrate treated by pulsating jets leads to the better adhesion of newly applied layers.
Numerical models of high pressure systems with an acoustic actuator. Numerical models of high pressure systems with an integrated acoustic actuator of high pressure pulsations were created. They allowed for the theoretical study of the processes of excitation and propagation of pressurised pulsations. The results of the numerical simulation of pressurised pulsations demonstrate that relatively complicated geometries with one or two L-bows or relatively long liquid waveguide allow for the propagation of pressure pulsations from the source to the nozzle. The intensity of pulsations upstream from the nozzle exit can be substantially affected by defining the dimensions of the separate parts of the high-pressure system and its tuning to resonance.
Abrasives for high-speed water jet technologies. Abrasive materials were evaluated from both mineralogical and petrological points of view, as well as from the point of view of their behaviour during the process of abrasive water jet generation and its action on the material to be cut. Methodologies for the assessment of the initial properties of abrasive concentrates, their cutting efficiency in reference materials, and wearing effects on the focusing tube, were developed together with the methodology of the description and morphological analysis of grains and cutting kerfs in macro- and micro-scales by image analysis.
The determination of biological noxiousness of respirable dust fraction resulting from disintegration of natural and synthetic abrasives and minerals of the quartz group during the application of an abrasive water jet represents another original result of the research. The work contributed to the formulation of both enduring problems and new themes for further research in the above mentioned area.
Application results. The results and knowledge attained were used in cooperation with industrial partners in a number of applications of the high-speed water jet technology. Tests of cutting and machining of the whole range of materials, the above-mentioned removal of layers in the rehabilitation of concrete structures or the removal and treatment of the surface layers of materials. The proposal of a technology of SS-23 missile grain disintegration using high-speed water jets or the proposal of a technology of non-firing liquidation of explosive charges situated in wells drilled for seismic surveys ranks among the special applications of water-jetting.
Based on the patents granted, an exclusive license agreement concerning the utilization of a patented solution of the generation of pressure pulsations in the high-pressure system to produce pulsating water was signed with a renowned German manufacturer of high-pressure equipment.
Other information
Recently solved projects ( PDF, 206 kB )
Selected publications ( PDF, 208 kB ) |
Patents ( PDF, 201 kB ) |