Solution: Denote by x the radial coordinate, r=1m the
inner radius, rY the radius of plastic zone, and R=2m the outer
radius of the tube, respectively. The elastic solution valid in the domain
satisfying
at the boundary takes the form
![\begin{displaymath}
\begin{array}{rcl}
\sigma_r&=&C[1-\left(\frac{R}{x}\right)^2...
...}{x}\right)^2]\\
\sigma_o&=&\nu(\sigma_r+\sigma_t)
\end{array}\end{displaymath}](img229.gif) |
(V.1) |
C is a constant to be determined from the yield condition
.
Substituting (V.1) into
von Mises' function
with x=rY, we get
![\begin{displaymath}
C(r_y)=\sigma_Y
\left[(1-2\nu)^2+3\left(\frac{R}{r_Y}\right)^4\right]^{-\frac{1}{2}}
\end{displaymath}](img232.gif) |
(V.2) |
A closed form solution in the plastic zone x<rY can only be obtained
for Tresca's condition or if
.
With von Mises's criterion and
we must resort to some simplifying assumptions.
The state of plane strain enforces
![\begin{displaymath}
\epsilon_o=\epsilon_o^e+\epsilon_o^p=
\frac{1}{E}[\sigma_o-\nu(\sigma_r+\sigma_t)]+\epsilon_o^p=0
\end{displaymath}](img234.gif) |
(V.3) |
At the elastic-plastic interface we have
,
which gives
 |
(V.4) |
If the loading approaches its plastic limit, the stress components cease
to change, therefore
and (V.3)
requires that
.
Using the Prandtl-Reuss
equations
 |
(V.5) |
and calculating the axial component of deviatoric stress tensor
we derive
 |
(V.6) |
Hence
 |
(V.7) |
Equations (V.4) and (V.7) suggest that the axial
stress is bounded in the plastic zone by
 |
(V.8) |
when
at x=rY whereas the upper bound
is approached in a limit as
.
Now, an approximation to the yielding function
is made by assuming
 |
(V.9) |
Setting
we obtain the yield condition in the form
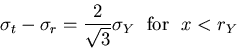 |
(V.10) |
In view of (V.4) the maximum deviation should be expected in
the vicinity of the elastic-plastic boundary. The error can easily be
estimated by inserting elastic solution (V.1), (V.2)
into the expression
![\begin{displaymath}
\sigma_t-\sigma_r=2\sigma_Y
\left[(1-2\nu)^2\left(\frac{R}{r_Y}\right)^4+3\right]^{-\frac{1}{2}}
~~\mbox{at}~~x=r_Y
\end{displaymath}](img247.gif) |
(V.11) |
Clearly, if
the right-hand sides of (V.10) and
(V.11) are coincident. In this example
,
R/rY=2/1.5, thus
 |
(V.12) |
Comparison with the factor
shows that (V.10) is a
good approximation to the yield condition at any point in the plastic
zone.
Solving the equilibrium equations
 |
(V.13) |
together with (V.10) and the boundary condition
yields
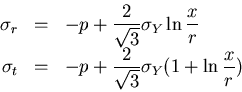 |
(V.14) |
The relationship between p and rY can be established by equating
(V.1)1 and (V.14)1 at x=rY, from which
![\begin{displaymath}
\frac{p}{\sigma_Y}=
\left[\left(\frac{R}{r_Y}\right)^2-1\rig...
...t)^4\right]^{-\frac{1}{2}}
+\frac{2}{\sqrt{3}}\ln\frac{r_Y}{r}
\end{displaymath}](img254.gif) |
(V.15) |
In this example we choose rY=1.5m, thus
MPa.
The estimate of
given by (V.9) is satisfactory for
the approximation of the yielding function but it would have been very
inaccurate for the calculation of
.
Fortunately, a
second-order correction can now be introduced by applying the
Prandtl-Reuss equations.
We use (V.9) and (V.14) as a first approximation to
compute the deviatoric stress
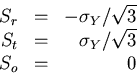 |
(V.16) |
Since the deviator is independent of plastic strain the Prandtl-Reuss
equations (V.5) may easily be integrated
 |
(V.17) |
By virtue of (V.3) the total strain components are computed as
![\begin{displaymath}
\begin{array}{rcl}
\epsilon_r &=&\displaystyle\frac{1-\nu^2}...
...\sigma_r]+\displaystyle\frac{\sqrt{3}}{2}\epsilon_p
\end{array}\end{displaymath}](img260.gif) |
(V.18) |
and substituted into compatibility condition
 |
(V.19) |
With the aid of (V.14) and after some manipulations the
differential equation for cumulated plastic strain
is
obtained
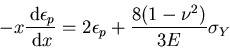 |
(V.20) |
Solving (V.20) with the boundary condition
we arrive at
![\begin{displaymath}
\epsilon_p=\frac{4(1-\nu^2)}{3E}\sigma_Y
\left[\left(\frac{r_Y}{x}\right)^2-1\right]
\end{displaymath}](img264.gif) |
(V.21) |
Once the cumulated plastic strain has been calculated we receive a better
estimate of
.
Integration of the Prandtl-Reuss equations
(V.5) leads to
![\begin{displaymath}
\epsilon_o^p=\frac{1}{\sigma_Y}\int_0^{\epsilon_p}
[\sigma_o...
...}{\sigma_Y}[\sigma_o-\textstyle\frac{1}{2}(\sigma_r+\sigma_t)]
\end{displaymath}](img266.gif) |
(V.22) |
Finally,
is resolved from (V.3) as
 |
(V.23) |
Note that
if
and
as
.
The results of numerical analysis and the analytical solution described
by eqns. (V.1),(V.2), (V.14) and
(V.23) are shown in figure.